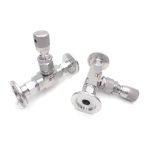
What Methods Are Used To Detect Leaks In Aerospace Vacuum Products?
1 Introduction
The development of aerospace products involves a large number of components or parts that require sealing performance, and even complete machine products, such as sealed cabins for manned spacecraft, satellite propellant fuel tanks, hydrogen-nickel batteries for spaceborne primary power supplies, and satellite communications Antennas, frequency standard light sources for timekeeping, and various other spaceborne instruments. The sealing performance of aerospace products is directly related to the launch success rate of the spacecraft and the service life of the orbit. Leakage detection runs through the entire process of aerospace product design, manufacturing, control of key process points, component performance, full star launch, launch and operation, and is an important means to ensure the sealing performance of aerospace products.
There are a variety of leak detection methods used in the aerospace field. The detection accuracy can be divided into two types: coarse inspection and fine inspection. The coarse inspection is mainly used for the detection of large leaks, and is suitable for the qualitative analysis of the sealing performance during the product development process. . The fine inspection is mainly used for the measurement and positioning of tiny leaks, which is suitable for the quantitative inspection of the sealing performance of products, and mainly introduces the fine leak detection method. Detailed inspection can be divided into helium mass spectrometry leak detection method, pressure change leak detection method and original working substance leak detection method from the measurement principle. The selection of the detection method needs to be comprehensively considered in terms of the sealing performance index requirements, volume size and structural complexity of the detected object, the safety of the inspection work, and the cost of inspection. Some experts believe that the helium mass spectrometry leak detection method should be preferred in the leak detection of aerospace products
- Analysis of helium mass spectrometry leak detection method
The helium mass spectrometry leak detection method is to use the helium mass spectrometer helium partial pressure measurement principle to realize the measurement of the helium leakage of the test piece. When there is a leak hole on the sealing surface of the test piece, the leaking gas helium and other components of the gas will leak out from the leak hole. The leaked gas enters the helium mass spectrometer leak detector. Selective identification capability only gives the partial pressure signal value of helium in the gas. On the basis of obtaining the signal value of helium gas, the leakage amount of the leak hole to helium can be obtained through the standard leak hole comparison method.
- Pressure change leak detection method
The pressure change leak detection method is to use the pressure change of the sealed container inside the tested product to achieve the measurement of the total leak rate of the tested product. The general leakage rate calculation formula is as follows:
Q = ΔP · V / Δt (1)
Where Q is the total leak rate of the tested product, Pa · m3 / s; ΔP is the amount of pressure change of the sealed container within the measurement time interval, Pa; V is the volume of the sealed container of the tested product, m3; Δt is the measurement time interval, s .
In general, according to the state of pressure increase or decrease, the pressure change method can be divided into static pressure increase method and static pressure decrease method. If the pressure before the measurement interval is less than the pressure after the measurement interval, it is called static The boost method, otherwise it is called the static buck method.
- The original working substance leak detection method
The original working substance leak detection is a method that uses the working medium filled inside the test piece as a leak gas to realize the leak rate measurement of the test piece. When the original working medium is used for leak detection, the inside of the test piece has been filled with leaking gas before the test, and no additional pressure charging equipment is required. If there is a leak in the test piece, the leaking gas inside the test piece will leak into the surrounding environment where the test piece is located through the leak hole, and the leaked gas will be introduced into the sample by atmospheric sampling or vacuum collection. The leak detection of the test piece can be realized inside the measurement sensor, and the frequently used sensor is a mass spectrometer.
The original working substance leak detection is generally suitable for occasions where the helium mass spectrometry leak detection method or the pressure change leak detection method cannot be used. In the field of aerospace products, the original working substance leak detection method is mainly used for launching satellite propellant, rocket common bottom dangerous gas, There are occasions such as nickel-hydrogen storage batteries and gas leak detection outside the space station, but with the development of the aerospace industry, we have reason to believe that the application of the original working substance leak detection method will also become more and more extensive
- Development trend of aerospace product leakage technology
With the continuous development of aerospace technology, especially the development of China’s manned spaceflight, long-term work requirements of space stations, lunar exploration projects and deep space exploration and other aerospace projects, the new requirements for spacecraft sealing and leak detection technology are bound to be put forward. Future leak detection technology should focus on the following aspects of research work:
(1) Research on leak detection technology of different sealing structures. The space station is a spacecraft for long-term human work. In order to ensure the long-term safe operation of the space station and ensure the safety of the astronauts, it is necessary to perform leak detection on the sealed capsule of the space station. The sealing structures required for space station leak detection include: cabin leak detection, space station double-channel static seal structure detection and cabin leak rate detection.
(2) Leak rate test for sealed containers with extremely small leak rates. In the missions of lunar exploration and deep space exploration, in order to ensure the authenticity of the component analysis of the “soil” on the surface of the planet, the detection sample packaging container with a very small leak rate is required, and the leak rate value is required to reach 10-13Pa · m3 / s. In order to meet the requirements for the detection of extremely small leak rates, it is necessary to study high-sensitivity detection devices and methods to evaluate sealed containers.
(3) Research on leak detection technology of original working medium of spacecraft sealing device in space environment. Through ground test and sealing evaluation, the leak detection and leakage rate measurement of the sealed container of the spacecraft with liquid medium during space operation are determined to ensure the long life index requirements of the spacecraft in orbit.
(4) Evaluation of the sealing performance of new materials, new structures and new processes used in the design of spacecraft seals. It is necessary to focus on the permeability test of space sealing materials to the actual gas in the cabin such as oxygen, nitrogen, air and helium. Comparison measurement of leakage rate under different sealing structures and different working conditions. Leakage performance change test after accelerated aging test of sealing materials and sealing structures, etc.
View more vacuum components with low price and free shipping all over the world.