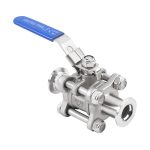
What are The Measurement Methods for Valve Machining Accuracy?
Valve machining accuracy adopts different measurement methods according to different machining accuracy content and accuracy requirements. Generally speaking, there are the following types of methods:
- According to whether the measured parameter is directly measured, it can be divided into direct measurement and indirect measurement.
Direct measurement: directly measure the measured parameter to obtain the measured size. For example, use calipers and comparators to measure. Indirect measurement: Measure geometric parameters related to the measured size, and obtain the measured size through calculation.
Obviously, direct measurement is more intuitive, and indirect measurement is more cumbersome. Generally, when the measured size or direct measurement fails to meet the accuracy requirements, indirect measurement has to be used.
- According to whether the reading value of the measuring tool directly represents the value of the measured size, it can be divided into absolute measurement and relative measurement.
Absolute measurement: The reading value directly indicates the size of the measured size, such as measuring with a vernier caliper.
Relative measurement: The reading value only indicates the deviation of the measured size from the standard quantity. If you use a comparator to measure the diameter of the shaft, you need to adjust the zero position of the instrument with a gauge block first, and then measure. The measured value is the difference between the diameter of the side shaft and the size of the gauge block. This is a relative measurement. Generally speaking, the relative measurement accuracy is higher, but the measurement is more troublesome.
- According to whether the measured surface is in contact with the measuring head of the measuring instrument, it is divided into contact measurement and non-contact measurement.
Contact measurement: The measuring head is in contact with the touched surface, and there is a mechanical measuring force. Such as measuring parts with a micrometer.
Non-contact measurement: The measuring head is not in contact with the surface of the measured part. Non-contact measurement can avoid the influence of measuring force on the measurement result. Such as the use of projection method, light wave interferometry and so on.
- According to the number of measurement parameters, it is divided into single measurement and comprehensive measurement.
Single measurement; each parameter of the tested part is measured separately.
Comprehensive measurement: measure the comprehensive index reflecting the relevant parameters of the part. For example, when measuring the thread with a tool microscope, the actual pitch diameter of the thread, the half-angle error of the tooth profile, and the cumulative error of the thread pitch can be measured separately.
Comprehensive measurement is generally more efficient and more reliable to ensure the interchangeability of parts, and is often used for inspection of finished parts. Single measurement can determine the error of each parameter separately, and is generally used for process analysis, process inspection, and measurement of specified parameters.
- According to the role of measurement in the processing process, it is divided into active measurement and passive measurement.
Active measurement: the workpiece is measured during the processing, and the result is directly used to control the processing of the part, so as to prevent the generation of waste in time.
Passive measurement: measurement performed after the workpiece is processed. This kind of measurement can only judge whether the processed part is qualified, and is limited to discovering and rejecting waste products.
- According to the state of the measured part in the measurement process, it is divided into static measurement and dynamic measurement.
Static measurement; the measurement is relatively static. Such as a micrometer to measure the diameter.
Dynamic measurement; the measured surface and the measuring head move relative to each other in the simulated working state during measurement. The dynamic measurement method can reflect the situation of the parts close to use, which is the development direction of measurement technology.
View more quality vacuum valves with low price and free shipping all over the world.