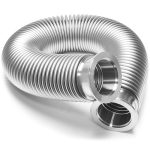
Performance Index of Bellows
Stiffness
The value of the load required to make a metal bellows or other elastic element to produce a unit displacement is called the stiffness of the element, and is generally expressed by “K”. If the elastic properties of the element are non-linear, the stiffness is no longer constant, but changes with increasing load. The elastic tolerance of bellows for general engineering can be limited within +/- 50%. The stiffness of the corrugated pipe is divided into axial stiffness, bending stiffness, torsional stiffness, etc. according to different load and displacement properties. In the application of bellows, most of the stress conditions are axial loads, and the displacement mode is linear displacement. The following are the main calculation methods for designing the axial stiffness of bellows:
- Energy method for calculating stiffness of bellows
- Empirical formula to calculate the stiffness of bellows
3. Numerical method for calculating the stiffness of bellows
4. EJMA standard stiffness calculation method
- Japan TOYO method for calculating stiffness
- US KELLOGG (new method) method for calculating stiffness
In addition to the above six methods of calculating stiffness, there are many other methods of calculating stiffness abroad that are not described here. Chinese mechanics have done a lot of work in the theoretical research and experimental analysis of bellows, and have achieved fruitful research results. The main research methods are:
(1) Perturbation method
(2) Initial parameter method for numerical integration
(3) Integral equation method
(4) Perturbed finite element method
All of the above methods can perform relatively accurate calculations on bellows. However, due to the application of deeper theories and methods of computational mathematics, it is difficult and difficult to master in engineering applications, and further popularization is needed.
Stiffness calculation of metal bellows and coil spring
In the process of use, when the rigidity is required to a large extent, and the rigidity of the metal bellows itself is relatively small, it may be considered to arrange a cylindrical coil spring in the inner cavity or the outside of the bellows. This can not only improve the stiffness of the entire elastic system, but also greatly reduce the error caused by hysteresis. The elastic performance of this elastic system mainly depends on the characteristics of the spring and the stability of the effective area of the bellows.
Bending stiffness of bellows
Stress calculation of bellows
As an elastic sealing part, a metal bellows must first meet the strength conditions, that is, its maximum stress does not exceed the allowable stress under given conditions. The allowable stress is obtained by dividing the ultimate stress by the safety factor. According to the working conditions of the bellows and the requirements for its use, the ultimate stress can be the yield strength, the critical stress when the bellows is unstable, or the fatigue strength. To calculate the maximum working stress of the bellows, the stress distribution in the wall of the bellows must be analyzed.
The stress on the bellows is caused by the pressure in the system and the deformation of the bellows. Pressure creates ring (circumferential) stress on the bellows, while radial films and bending stresses occur on the side walls, troughs, and crests of the wave. A thin shell that cannot be bent is sometimes called a thin film, and the stress calculated by ignoring bending is called a thin film stress. When the bellows deforms, it generates radial film stress and bending stress. When the bellows work, some bear the internal pressure and some bear the external pressure, such as bellows expansion joints and metal hoses. In most cases, the bellows bears the inner pressure. The bellows used for valve stem sealing are generally used. Withstand external pressure Here we mainly analyze the stress of the bellows when it is under internal pressure. The ability of the bellows to withstand external pressure is generally higher than its ability to withstand internal pressure. With the wide application of bellows, people have carried out a lot of analysis and experimental verification of the stress of the bellows, and put forward many calculation formulas, calculation programs and charts for engineering design. However, some methods are inconvenient to use due to complicated diagrams or programs, and some methods assume conditions that are either too simplified or too ideal, making it difficult to ensure safety and reliability in use, and many methods have not been accepted by the engineering community. Therefore, there are few methods that truly meet practical requirements. There are two commonly used methods:
- Numerical method for calculating stress of bellows
It is assumed that all the corrugations of the bellows are in the same condition, and only a single half wave of the bellows ripples is studied in the calculation. In this way, the end ripple is not considered in the study, although the boundary conditions of the end ripple are different from the middle ripple. The numerical method is based on E. Lesnell solved the nonlinear equations listed in the case of the axially symmetric deformation of the rotating shell with variable wall thickness. E. in derivation In the Lesnell equation, the general assumptions of the thin shell theory are applied, including: the assumption that the thickness is small compared with the principal radius of curvature of the torus; the assumption that the material is homogeneous and isotropic. Adopting the above assumptions will also bring some errors to the calculation. Because in the manufacture of corrugated pipes, the rolling, drawing and subsequent corrugated plastic forming of the tube blank will cause anisotropy and non-uniformity in the mechanical properties of the material.
- American EJMA Stress Calculation Method
Calculation of effective area of bellows
The effective area is one of the basic performance parameters of the bellows. It represents the ability of the bellows to convert pressure into concentrated force. In the case of using the bellows to convert pressure into concentrated force output, the effective area is an important parameter.
When a bellow is used in a force-balanced instrument, the stability of its effective area will directly affect the accuracy of the instrument. Therefore, in this case, not only the reasonable effective area of the bellows is required, but also the effective area does not change with the working conditions during the working process.
- The concept of effective area and changes in effective area
The effective area is an equivalent area, and pressure exerts equal axial force on this area. In general, as the internal pressure increases, the effective area of the bellows becomes smaller, and as the external pressure increases, the effective area becomes larger.
- Volume effective area of bellows
Under the action of external force or pressure difference, the ratio of the volume change of the bellows to the corresponding effective length is called the volume effective area.
3. Calculation of effective area of bellows
The requirements for the effective area of the bellows and their calculation methods depend on the purpose of the bellows. If the bellows is used as an elastic seal or thermal compensation of the pipeline, the meaning of the effective area is only used to calculate the axial force when the bellows is formed and the thrust in the system. There are some differences between the calculated value of the effective area of the bellows and the measured value. In general, using a special formula to calculate the effective area of the bellows can meet the needs.
When the bellows is used for force balancing instruments and field platforms that need to convert pressure to force, its effective area should be accurately determined and measurements should be taken one by one.
Sensitivity
The extravagant amount of metal bellows and other elastic components under unit load is called the sensitivity of the component. Stiffness and sensitivity are the main functional parameters of bellows and other elastic components, but they are two different ways of expressing the same usage characteristics. For different occasions, to facilitate the analysis of the problem, any of these parameters can be used.
Effective area
For an elastic element that achieves pressure-to-force or force-to-pressure conversion, another important functional indicator is the effective area. The effective area refers to the amount of elastic force that can be converted into a concentrated force under the unit pressure when its displacement is zero.
Service life
There are two states when the elastic element works; one is working under a certain load and displacement, and the load and displacement are kept constant or rarely changed, which is called static work; the other use case is load and displacement The cycle changes back and forth. The component is in cyclic operation. Due to different working conditions, the modes of component damage or failure are also different. The instrument’s elastic sensitive components work in the elastic range, basically in a static working state, and have a long service life, generally reaching tens of thousands to hundreds of thousands of times. The bellows components used in engineering sometimes work in the elastoplastic range or alternating stress state, and the life is only hundreds of dry times. The components must be given a permissible working life when they are cycled, and the number of cycles, time, and frequency must be specified.
The rated life of an elastic component is the expected life set during the design of the component. It is required that the component should not be fatigued, damaged or failed during this period.
Tightness
Hermeticity refers to the performance of the component to ensure no leakage under a certain internal and external pressure difference. When the bellows-type components work, the inner cavity is filled with a gas or liquid medium and has a certain pressure, so the tightness must be guaranteed. Testing methods for air tightness include air tightness test, leak test, liquid pressure test, soap water or helium mass spectrometer leak detector.
Natural frequency
The elastic components used in industry often have a certain degree of vibration in the working environment, and some components are used as vibration isolation components. It is under vibration. For elastic components applied under special conditions, the natural frequency of the component (especially the fundamental frequency) must be prevented from being close to the vibration frequency of any vibration source in the system to avoid damage caused by resonance. Corrugated tube components have been widely used in various fields. In order to avoid damage to the resonance surface of the corrugated tube, the natural frequency of the corrugated tube should be lower than the vibration frequency of the system, or at least 50% higher than the vibration frequency of the system.
Operating temperature
Metal bellows components have a wide temperature range, and are generally given before the design and manufacture of elastic components. For some special-purpose bellows, the inner cavity passes liquid oxygen (-196 ° C) or lower temperature liquid nitrogen, and the pressure resistance is up to 25MPa. Large-scale corrugated expansion joints for connection of pipe network systems (the nominal diameter sometimes exceeds lm) require a pressure of 4MPa, a temperature resistance of 400 ° C, and a certain degree of corrosion resistance. The temperature adaptability of the elastic element depends on the temperature resistance of the elastic material used. Therefore, according to the operating temperature range of the elastic element, an elastic material with suitable temperature performance parameters can be used to process and produce qualified bellows components.