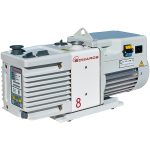
Failure Analysis of Water Ring Vacuum Pump
Aiming at the current operating status of the 2BE1-403-0E water ring vacuum pump, the system analyzes the causes of frequent failures of the water ring vacuum pump, and provides the experience of water ring vacuum pump bearing failure analysis for your reference.
1 Introduction
BE2BE1-403-0E water ring vacuum pump is mainly used to remove the gas in the horizontal belt filter, and provide a vacuum environment for the filter. If the vacuum pump cannot operate normally, the corresponding filter will not work. During the operation of the vacuum pump, problems such as corrosion leakage of the cylinder and the side plate, low vacuum, insufficient flow, etc. often cause the technical specifications of the equipment to fail, fail to meet the process requirements, and lead to frequent shutdown and maintenance, which directly affects the entire Normal production of the device. For this reason, in view of this situation, in order to solve the bottleneck of the device, the 2BE1-403-0E water ring vacuum pump reconstruction was used as a technical research and transformation project.
- Equipment parameters and working principle
2.1 Performance parameters of vacuum pump
The performance parameter table of vacuum pump is listed in Table 1. The conveying medium is the gas in the horizontal belt filter. The working fluid is chemical circulating water of the pipe network.
2.2 2BE1-403-0E water ring vacuum pump working principle
The water ring vacuum pump is mainly composed of the end cover on both sides, the side plate next to the end cover, the middle cylinder and the middle impeller.
2.3 Working principle of 2BE1-403-0E water ring vacuum pump
First, about 1/3 of the working fluid is injected into the cylindrical pump cylinder of the water ring vacuum pump. The impeller is eccentrically installed in the pump cylinder. When the impeller rotates clockwise in the figure, the water is thrown around by the impeller, forming A closed water ring of approximately equal thickness determined by the shape of the pump cavity. Due to the centrifugal force, a crescent-shaped space is formed between the impeller hub and the water ring, and this space is divided into several small cavities equal to the number of blades by the impeller. If the 6 o’clock direction of the impeller is used as the reference point, then the volume of the closed cavity at the first 180 ° of the impeller changes from small to large, forming a negative pressure. At this time, the gas is sucked in through the suction port, and when the suction ends, the small cavity is isolated from the suction port. When the impeller continues to rotate, after the 6 o’clock reference direction, the small cavity starts to change from large to small, so that the gas is compressed; when the small cavity communicates with the exhaust port, gas and water enter from the exhaust hole through the joint along the exhaust pipe. In the gas-water separator, the gas is automatically released by the gas discharge pipe after the separation, and the working fluid flows back to the cavity for repeated use.
- Investigation of the status of vacuum pumps
According to the equipment disassembly inspection analysis, the failure types are roughly divided into the following categories.
(1) The side plate and cylinder are corroded and deformed seriously, and sometimes even the perforation leaks.
(2) The vacuum degree of the water ring vacuum pump is too low to meet the production process requirements of the filter.
(3) In recent years, the flow rate of water ring vacuum pumps has been seriously insufficient, resulting in the failure of other units to operate at full capacity, and ultimately affecting the catalyst output.
(4) In the long-term operation of the equipment, the wear of the bearings at both ends of the vacuum pump or the wear of the rotor shaft head often causes the bearings to run, the equipment vibrates, the sound is loud, and it can not operate normally in severe cases.
- Equipment failure cause analysis
4.1 Corrosion and deformation analysis of cylinder and side plate
BE2BE1-403-0E vacuum pump is a water ring gas pump. Its barrel and side plates are made of carbon steel steel plate and welded. The corrosion rate of carbon steel in pure water is small, but as long as the water contains a small amount of acid ions, the corrosion rate of the material will be significantly accelerated. The horizontal belt filter of the catalyst device, some substances in the NY molecular sieve filter cake filtered during the production process will decompose and emit sulfur trioxide, hydrogen chloride gas. These acid gases are sucked into the pump cavity by the water ring vacuum pump together with other gases. The working fluid added to the vacuum pump is chemical water in the pipe network, which contains sulfate ions. The working fluid containing sulfuric acid ions reacts with sulfur trioxide and hydrogen chloride in the working medium to generate dilute sulfuric acid and hydrochloric acid, which directly corrode the cylinder and the side plate. The reaction mechanism of the corrosion fitting is as follows.
Fe + 2HCl = FeCl2 + H2
Fe + H20 + SO3 = FeSO4 + H2 (iron)
On the other hand, the working medium sucked by the vacuum pump is mixed with a solid particulate catalyst semi-finished product. These white solid particles are mixed with the acidic liquid produced by the chemical reaction in the cavity to form a strong acidic thin slurry. This thin slurry is driven by the impeller to rotate at high speed, and the loosely structured FeCl2 and FeSO4 are quickly worn away. This kind of wear and tear also damages the non-corroded carbon steel material. The acid corrosion and solid particle wear work together to make the cylinder and the side plate continue to be non-uniformly thinned until the perforation leaks.
2BE1-403-0E water ring vacuum pump has a design ultimate vacuum of 98 kPa, which was generally low before the transformation.
4.2. Analysis of the vacuum degree of the vacuum pump is too low
Floats up and down at 70 KPa. Eliminating the aging factors of the equipment is mainly due to acid corrosion and solid particle wear, which increases the distance between the edge of the impeller and the cylinder and the side plate, destroys the geometry of the compression channel, and causes turbulence and backflow. The geometry of the vacuum pump flow channel is determined through simulation calculations and repeated experiments. Once the flow channel is damaged, the efficiency of the vacuum pump will drop sharply, which will directly cause the vacuum of the vacuum pump to fail to meet the standards.
4.3. Analysis of serious insufficient flow of water ring vacuum pump
Due to the fouling of the vacuum pump casing for a long time, very thick dirt is formed and the pump casing space is blocked, as shown in Figure 5. In the dirt, acid corrosion and solid particles wear out, destroying the geometry of the pump compression flow channel, causing turbulence and backflow. A considerable part of the energy input from the motor shaft end is converted into the internal energy of the conveying medium instead of the kinetic energy in the form of a fierce collision of liquid in the pump cavity. In addition, due to the corrosion of the acid mud, the flow channel of the pump is uneven, and a large amount of solid particles adhere to the inner wall, which reduces the flow cross-section. In the end, the flow of the water ring vacuum pump is seriously insufficient, which delays production.
4.4. Water ring vacuum pump bearings are frequently replaced, resulting in high operating noise
The vacuum pump cylinder and the inner wall of the side plate are severely corroded and worn and very rough. This increases the distance between the edge of the impeller, the barrel and the side plate, and destroys the originally stable laminar flow ring. The white acid thin mud wrapped around the medium gas violently collided in the cylinder in the form of turbulence, which caused the vacuum pump to vibrate violently, damage the bearings and generate noise.
- Examples of analyzing bearing failure
On March 9, 2011, during the monitoring process, the monitoring personnel found that the bearing housing at the rear end of the pump made an intermittent “booming” abnormal noise, with a high temperature of 61℃. Analysis of the cause of the failure, observe the vibration value and CF value: The peak value of the OA value in the vertical direction of the front and rear ends is as high as 28. 31 mm / s, and the front bearing is worn.
Observe and analyze the vertical, horizontal and axial spectrum of the free end of the vacuum pump.
6 Conclusion
In the long-term use of the 2BE1-403-0E water ring vacuum pump, this type of failure often occurs. After continuous analysis and targeted treatment of the failure, the operating cycle of the equipment can be extended and the inspection and maintenance cost can be greatly reduced.