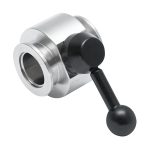
Detailed Solenoid Valve
Electromagnetic valve (Electromagnetic valve) is an industrial equipment controlled by electromagnetic. It is an automation basic component used to control fluid. It belongs to actuator and is not limited to hydraulic and pneumatic. Used in industrial control systems to adjust the direction, flow, speed and other parameters of the medium. The solenoid valve can cooperate with different circuits to achieve the desired control, and the accuracy and flexibility of the control can be guaranteed. There are many kinds of solenoid valves. Different solenoid valves play a role in different positions of the control system. The most commonly used ones are check valves, safety valves, directional control valves, and speed control valves.
working principle
There is a closed cavity in the solenoid valve with through holes at different positions. Each hole is connected to a different oil pipe. In the middle of the cavity is a piston. There are two electromagnets on both sides. Which side of the magnet coil will be attracted to the valve body when it is energized. On the other hand, by controlling the movement of the valve body to open or close the different oil discharge holes, and the oil inlet is normally open, the hydraulic oil will enter the different oil discharge pipes, and then the piston of the cylinder is pushed by the oil pressure. Drive the piston rod, and the piston rod drives the mechanical device. In this way, the mechanical movement is controlled by controlling the current on and off of the electromagnet.
2 main categories
- The solenoid valve is divided into three categories in principle:
1) Direct-acting solenoid valve:
Principle: When energized, the electromagnetic coil generates electromagnetic force to lift the closing member from the valve seat, and the valve opens; when the power is off, the electromagnetic force disappears, and the spring presses the closing member on the valve seat and the valve closes.
Features: It can work normally under vacuum, negative pressure and zero pressure, but the diameter generally does not exceed 25mm.
2) Step-by-step direct-acting solenoid valve:
Principle: It is a principle that combines direct action and pilot type. When there is no pressure difference between the inlet and the outlet, the electromagnetic force directly lifts the pilot small valve and the main valve closing member upwards in turn, and the valve opens. When the inlet and outlet reach the starting pressure difference, after power on, the electromagnetic force pilots the small valve, the pressure in the lower chamber of the main valve rises, and the pressure in the upper chamber drops, so that the pressure difference pushes the main valve upward; when the power is off, the pilot valve uses a spring The force or medium pressure pushes the closing piece and moves downward to close the valve.
Features: It can be operated under zero pressure difference or vacuum and high pressure, but the power is large, and it must be installed horizontally.
3) Pilot solenoid valve:
Principle: When energized, the electromagnetic force opens the pilot hole, the pressure in the upper chamber drops rapidly, and a high pressure difference is formed around the closing part. The fluid pressure pushes the closing part to move upward, and the valve opens; when the power is off, the spring force controls the pilot The hole is closed, and the inlet pressure quickly passes through the bypass hole to form a low and high pressure difference around the valve closing member. The fluid pressure pushes the closing member to move downward to close the valve.
Features: The upper limit of the fluid pressure range is high and can be installed arbitrarily (customization is required) but must meet the fluid pressure difference conditions.
- The solenoid valve is divided into six sub-categories from the difference in valve structure and material and principle: direct-acting diaphragm structure, stepwise direct-acting diaphragm structure, pilot diaphragm structure, direct-acting piston structure, Step-by-step direct-acting piston structure, pilot piston structure.
- Solenoid valves are classified according to their functions: water solenoid valves, steam solenoid valves, refrigeration solenoid valves, cryogenic solenoid valves, gas solenoid valves, fire solenoid valves, ammonia solenoid valves, gas solenoid valves, liquid solenoid valves, micro solenoid valves, Pulse solenoid valve, hydraulic solenoid valve normally open solenoid valve, oil solenoid valve, DC solenoid valve, high pressure solenoid valve, explosion-proof solenoid valve, etc.
3 Type selection attention
Selection basis
The selection of solenoid valve should first follow the four principles of safety, reliability, applicability, and economy in order, and then according to the six aspects of on-site working conditions (i.e. pipeline parameters, fluid parameters, pressure parameters, electrical parameters, action methods, Special requirements for selection).
Selection basis:
- Select the solenoid valve according to the pipeline parameters: diameter specification (namely DN), interface mode
1) Determine the diameter (DN) size according to the pipe inner diameter size or flow requirements on site;
2) Interface mode, generally >DN50 should choose flange interface, ≤DN50 can be freely selected according to user needs.
- Choose the solenoid valve according to the fluid parameters: material, temperature group
1) Corrosive fluid: Corrosion-resistant solenoid valve and all stainless steel should be selected; Edible ultra-clean fluid: Food-grade stainless steel solenoid valve should be selected;
2) High temperature fluid: choose solenoid valves made of high temperature resistant electrical materials and sealing materials, and choose piston structure types;
3) Fluid state: large to gaseous, liquid or mixed state, especially when the diameter is larger than DN25, it must be distinguished;
4) Fluid viscosity: usually below 50cSt, it can be arbitrarily selected. If it exceeds this value, a high-viscosity solenoid valve should be used.
- Choose solenoid valve according to pressure parameters: principle and structure variety
1) Nominal pressure: This parameter has the same meaning as other general valves, and it is determined according to the nominal pressure of the pipeline;
2) Working pressure: If the working pressure is low, the principle of direct acting or stepwise direct acting must be used; when the minimum working pressure difference is above 0.04Mpa, direct acting, stepwise direct acting, and pilot operated are all available.
- Electrical selection: It is more convenient to choose AC220V and DC24 for voltage specifications.
- Choose according to the length of continuous working time: normally closed, normally open, or continuously energized
1) When the solenoid valve needs to be opened for a long time, and the duration is longer than the closing time, the normally open type should be selected;
2) If the opening time is short or the opening and closing time is not long, choose the normally closed type;
3) However, for some working conditions used for safety protection, such as furnace and kiln flame monitoring, the normally open type cannot be selected, and the long-term power-on type should be selected.
- Select auxiliary functions according to environmental requirements: explosion-proof, non-return, manual, waterproof, mist, water shower, diving.
Selection principle
safety:
- Corrosive medium: Plastic solenoid valve and all stainless steel should be used; for strong corrosive medium, the isolation diaphragm type must be used. For neutral media, a solenoid valve with a copper alloy as the valve housing material should also be used, otherwise, rust debris will often fall off the valve housing, especially in occasions where the action is not frequent. The valve for ammonia cannot be made of copper.
- Explosive environment: products of corresponding explosion-proof grade must be selected, and waterproof and dust-proof products should be selected for outdoor installation or dusty occasions.
- The nominal pressure of the solenoid valve should exceed the highest working pressure in the pipe.
applicability:
- Medium characteristics
1) Choose different types of solenoid valves for quality gas, liquid or mixed state;
2) Products with different specifications of medium temperature, otherwise the coil will burn out and the seal will be aging, which will seriously affect the life span;
3) Medium viscosity, usually below 50cSt. If it exceeds this value, if the diameter is greater than 15mm, use a multifunctional solenoid valve; if the diameter is less than 15mm, use a high viscosity solenoid valve.
4) When the cleanliness of the medium is not high, a recoil filter valve should be installed in front of the solenoid valve. When the pressure is low, a direct-acting diaphragm solenoid valve can be used;
5) If the medium circulates directionally and does not allow backflow, bidirectional circulation is required;
6) The temperature of the medium should be selected within the allowable range of the solenoid valve.
- Pipeline parameters
1) Choose valve port and model according to medium flow requirements and pipe connection mode;
2) Select the nominal diameter according to the flow rate and the valve Kv value, and the same pipe inner diameter can also be selected;
3) Working pressure difference: if the minimum working pressure difference is above 0.04Mpa, the indirect pilot type can be selected; if the minimum working pressure difference is close to or less than zero, the direct-acting type or the stepwise direct type must be selected.
- Environmental conditions
1) The maximum and minimum temperature of the environment should be selected within the allowable range;
2) In the environment where the relative humidity is high and there are water drops and rain, etc., the waterproof solenoid valve should be selected;
3) Special varieties should be selected for occasions where there are frequent vibrations, bumps and shocks in the environment, such as marine solenoid valves;
4) For use in corrosive or explosive environments, the corrosion-resistant type should be selected first according to the safety requirements;
5) If the environmental space is restricted, a multifunctional solenoid valve should be used, because it saves the bypass and three manual valves and is convenient for online maintenance.
- Power conditions
1) According to the type of power supply, select AC and DC solenoid valves respectively. Generally speaking, AC power is easy to access;
2) For voltage specifications, choose AC220V.DC24V as priority;
3) The power supply voltage fluctuation is usually +%10%.-15% for AC, and DC allows about ±%10. If it is out of tolerance, voltage stabilization measures must be taken;
4) The rated current and power consumption should be selected according to the power supply capacity. It should be noted that the VA value is higher when the AC starts, and the indirect pilot solenoid valve should be preferred when the capacity is insufficient.
- Control accuracy
1) Ordinary solenoid valves have only two positions, open and closed, and multi-position solenoid valves are required when the control accuracy is high and the parameters are stable;
2) Action time: refers to the time from when the electrical signal is switched on or off to the completion of the main valve action;
3) Leakage: The leakage value given on the sample is a common economic grade.
reliability:
- Working life, this item is not included in the factory test item, it belongs to the type test item. In order to ensure quality, brand-name products from regular manufacturers should be selected.
- Work system: divided into long-term work system, repeated short-time work system and short-time work system. If the valve is opened for a long time and only closed for a short time, a normally open solenoid valve should be used.
- Operating frequency: When the operating frequency is high, the structure should be a direct-acting solenoid valve, and the power supply should be preferably AC.
- Action reliability
Strictly speaking, this test has not been officially included in the professional standards for solenoid valves in China. To ensure quality, brand-name products from regular manufacturers should be selected. In some occasions, the number of actions is not many, but the reliability requirements are high, such as fire protection, emergency protection, etc., must not be taken lightly. Especially important, two insurances should be used in conjunction.
Economy:
It is one of the selected standards, but it must be economical on the basis of safety, applicability and reliability.
Economy is not only the price of the product, but also its function and quality, as well as the cost of installation, maintenance and other accessories.
More importantly, the cost of a solenoid valve in the entire automatic control system in the entire automatic control system and even in the production line is very small, and the damage caused by the wrong choice of small and cheap is huge.
4 Installation attention
- When installing, pay attention that the arrow on the valve body should be consistent with the flow direction of the medium. Do not install in a place with direct dripping or splashing water. The solenoid valve should be installed vertically upwards;
- The solenoid valve should be guaranteed to work normally within the 15%-10% fluctuation range of the rated voltage of the power supply voltage;
- After the solenoid valve is installed, there must be no reverse pressure difference in the pipeline. And it needs to be energized several times to make it suitable for temperature before it can be put into use;
- Thoroughly clean the pipeline before installing the solenoid valve. The medium should be free of impurities. Install a filter before the valve;
- When the solenoid valve fails or is cleaned, to ensure the system continues to run, a bypass device should be installed.
5 Troubleshooting
- The solenoid valve does not work after being energized
Check whether the power wiring is bad → rewire and connect the connector
Check whether the power supply voltage is within the ± working range-→ adjust to the normal position range
Whether the coil is unsoldered → re-soldered
Coil short circuit → replace the coil
Whether the working pressure difference is not appropriate → adjust the pressure difference → or replace the commensurate solenoid valve
The fluid temperature is too high → replace the appropriate solenoid valve
Impurities cause the main valve core and moving iron core of the solenoid valve to jam → clean, if the seal is damaged, replace the seal and install the filter
The viscosity of the liquid is too high, the frequency is too high, and the life is reached → replace the product
- The solenoid valve cannot be closed
The seal of the main spool or iron core is damaged → replace the seal
Whether the fluid temperature and viscosity are too high → replace the solenoid valve of the corresponding port
Impurities enter the solenoid valve core or moving iron core → clean
Spring life has reached or deformed → replace
Orifice balance hole blocked → timely cleaning
The working frequency is too high or the service life is up → change the product or update the product
- Other situations
Internal leakage → check whether the seal is damaged, whether the spring is poorly assembled
External leakage → loose connection or damaged seal → tighten the screw or replace the seal
There is noise when energized → The firm part on the head is loose, tighten it. If the voltage fluctuation is not within the allowable range, adjust the voltage. If the suction surface of the iron core is impurity or uneven, clean or replace it in time.
6 sealing material
There are three most commonly used sealing materials for solenoid valves.
NBR nitrile butadiene rubber
It is produced by emulsion polymerization of butadiene and acrylonitrile. Nitrile rubber is mainly produced by low-temperature emulsion polymerization. It has excellent oil resistance, high wear resistance, good heat resistance, and strong adhesion. Its disadvantages are poor low temperature resistance, poor ozone resistance, poor electrical properties, and slightly lower elasticity.
In addition, it also has good water resistance, air tightness and excellent bonding properties. Widely used in the manufacture of various oil-resistant rubber products, a variety of oil-resistant gaskets, gaskets, casings, flexible packaging, flexible hoses, printing and dyeing rubber rollers, cable rubber materials, etc., becoming indispensable in industries such as automobiles, aviation, petroleum, and copying The elastic material.
Nitrile rubber has excellent oil resistance, its oil resistance is second only to polysulfide rubber and fluorine rubber, and has abrasion resistance and air tightness. The disadvantage of nitrile rubber is that it is not resistant to ozone and aromatics, halogenated hydrocarbons, ketones and ester solvents, and is not suitable for insulating materials.
The main purpose
Nitrile rubber is mainly used to make oil-resistant products, such as oil-resistant pipes, tapes, rubber diaphragms and large oil sacs. It is often used to make various oil-resistant molded products, such as O-rings, oil seals, cups, diaphragms, valves, bellows, etc. It is also used to make rubber sheets and wear-resistant parts.
EPDM (Ethylene-Propylene-Diene Monomer)
EPDM rubber is a terpolymer of ethylene, propylene and non-conjugated diene. Commercial production began in 1963. The annual world consumption is 800,000 tons. The main feature of EPDM is its superior resistance to oxidation, ozone and corrosion. As EPDM belongs to the polyolefin family, it has excellent vulcanization properties. Among all rubbers, EPDM has the lowest specific gravity. It can absorb a large amount of filler and oil without affecting the characteristics. Therefore, low-cost rubber compounds can be produced.
Molecular structure and characteristics: EPDM is a terpolymer of ethylene, propylene and non-conjugated diene. Diene has a special structure, and only one of the two bonds can be copolymerized, and the unsaturated double bond is mainly used as a cross-chain. The other unsaturated one will not become the main polymer chain, only the side chain. The main polymer chain of EPDM is fully saturated. This feature makes EPDM resistant to heat, light, oxygen, and especially ozone. EPDM is essentially non-polar, has resistance to polar solutions and chemicals, has low water absorption, and has good insulation properties.
Features
- Low density and high filling;
- Aging resistance;
- Corrosion resistance;
- Water vapor resistance;
- Superheated water resistance;
- Electrical performance;
- Flexibility;
- Adhesion.
VITON Fluorine Rubber (FKM)
The fluorine-containing rubber in the molecule has various types depending on the fluorine content, that is, the monomer structure; the fluorine hexafluoride rubber has better high temperature resistance than silicone rubber, chemical resistance, and resistance to most oils and solvents (ketones, esters) Except for class), weather resistance, ozone resistance are good, but cold resistance is poor; generally widely used in automobile, motorcycle, B and other products, chemical plant seals, the operating temperature range -20 ℃ ~ 260 ℃, when used at low temperatures There is a low temperature resistant type that can be applied to -40℃, but the price is higher.
7 main differences
The difference between electric valve and solenoid valve:
The solenoid valve is a solenoid coil that generates a magnetic attraction to overcome the pressure of the spring to drive the spool action after the solenoid is energized. It is a solenoid coil with simple structure and low price, which can only be switched;
The electric valve drives the valve stem through an electric motor to drive the spool to move. The electric valve is divided into a shut-off valve and a regulating valve. The shut-off valve is a two-position work that is fully open and fully closed. The regulating valve is equipped with an electric valve positioner, and the valve is dynamically stabilized in a position through closed-loop adjustment.
Use comparison of electric valve and solenoid valve:
Solenoid valve: used for on-off control of liquid and gas pipelines, two-position DO control. Generally used for the control of small pipelines.
Electric valve: It is used to adjust the analog quantity of the pipe medium flow of liquid, gas and wind system, which is AI control. In the control of large valves and wind systems, electric valves can also be used for two-position switch control.
Solenoid valve: It can only be used as a switch value. It is DO control and can only be used for small pipeline control. It is common in pipelines of DN50 and below.
Electric valve: It can have AI feedback signal and can be controlled by DO or AO. It is more common in large pipelines and air valves. [1]
- Switch form:
The solenoid valve is driven by a coil and can only be opened or closed, and the action time is short when switching.
The driving of the electric valve is generally by a motor, and it takes a certain amount of time to complete the opening or closing action, which can be adjusted.
- Nature of work:
Solenoid valves generally have a small flow coefficient and a small difference in working pressure. For example, the general 25-caliber solenoid valve has a much smaller flow coefficient than the 15-caliber electric ball valve. The solenoid valve is driven by the solenoid coil, which is easily damaged by voltage shock. It is equivalent to the function of a switch, which is two functions of on and off.
Electric valves are generally driven by motors, which are relatively resistant to voltage shocks. Solenoid valves are quick-opening and quick-closing. They are generally used in places where small flow and small pressure are required, and the electric valve is reversed where high switching frequency is required. The opening degree of the electric valve valve can be controlled, and the state is open, closed, half-open and half-closed, which can control the flow of the medium in the pipeline, but the solenoid valve cannot meet this requirement.
Solenoid valves can generally be reset when power is off. For such functions, electric valves need a reset device. [2]
- Applicable process:
Solenoid valve is suitable for some special process requirements, such as leakage, special fluid medium, etc., and the price is more expensive.
Electric valves are generally used for adjustment, and there are also switching values, such as the end of a fan coil.
8 main features
- External leakage is blocked, internal leakage is easy to control, safe to use
Internal and external leakage is an element that endangers safety. Other automatic control valves usually extend the valve stem, and the rotation or movement of the valve core is controlled by an electric, pneumatic, or hydraulic actuator. This must solve the problem of external leakage of the dynamic seal of the long-term valve stem; only the solenoid valve uses electromagnetic force to act on the iron core sealed in the magnetic isolation sleeve of the electric control valve. There is no dynamic seal, so the external leakage is easy to block. . The torque control of the electric valve is not easy, and it is easy to produce internal leakage, or even pull off the head of the valve stem; the structure of the solenoid valve is easy to control the internal leakage until it drops to zero. Therefore, the solenoid valve is particularly safe to use, especially suitable for corrosive, toxic or high and low temperature media.
- The system is simple, just connect to the computer, the price is low
The solenoid valve itself is simple in structure and low in price. It is easier to install and maintain than other types of actuators such as control valves. What’s more obvious is that the composed automatic control system is much simpler and the price is much lower. Since the solenoid valve is controlled by a switch signal, it is very convenient to connect with an industrial computer. In today’s era when computers are popular and prices drop sharply, the advantages of solenoid valves are even more obvious.
- Express action, small power, light appearance
The response time of the solenoid valve can be as short as a few milliseconds, even the pilot solenoid valve can be controlled within tens of milliseconds. Because of its self-contained circuit, it is more sensitive than other automatic control valves. A properly designed solenoid valve coil has low power consumption and is an energy-saving product; it can also automatically maintain the valve position only by triggering the action, and it does not consume electricity at all. The solenoid valve is small in size, which saves space and is light and beautiful.
- The adjustment accuracy is limited and the applicable medium is limited
Solenoid valves usually have only two states on and off, and the spool can only be in two extreme positions and cannot be adjusted continuously, so the adjustment accuracy is still limited.
Solenoid valves have high requirements for the cleanliness of the medium, and the granular medium cannot be used. If it is impurities, it must be filtered out first. In addition, viscous media cannot be applied, and the viscosity range of the media for specific products is relatively narrow.
- Diverse models and wide applications
Although solenoid valves have inherent deficiencies, their advantages are still outstanding, so they are designed into a variety of products to meet various needs and have a wide range of uses. The advancement of solenoid valve technology also revolves around how to overcome congenital shortcomings and how to make better use of inherent advantages.
9 relevant regulations
- Points for product selection
1) The main control parameters of the solenoid valve are the diameter, the design nominal pressure, the allowable temperature range of the medium, and the interface size.
2) Solenoid valves use electromagnets to drive the opening and closing of the valve. It is usually used in two-position control with a diameter of less than 40mm, especially for connecting, cutting off or switching gas and liquid circuits.
3) The sealing performance of the valve is one of the main indicators for evaluating the quality of the valve. The sealing performance of the valve mainly includes two aspects, namely internal leakage and external leakage. Internal leakage refers to the degree of sealing between the valve seat and the closing member to the medium. External leakage refers to the leakage of the valve stem packing part, the leakage of the middle port gasket and the leakage of the valve body due to casting defects. Leakage is not allowed.
4) The main advantages of solenoid valves are small size, reliable action, convenient maintenance and low price. When choosing, you need to pay attention to choosing the normally open or normally closed type according to the process requirements.
- Key points of construction and installation
1) The installation position and height of the valve must meet the design requirements of the port direction, and the connection should be firm and tight.
2) The valve must be visually inspected before installation. The nameplate of the valve should comply with the current national standard GB12220 “General Valve Marking”.
- Implementation standards
Product Standards:
China’s solenoid valve product industry standard “Solenoid valve for industrial process control system (JB/T7352-2010)”
GB/T13927-92 “General Valve Pressure Test”
JB/T8528-1997 “Technical Conditions for Common Valve Electric Devices”
GB12220-89 “General Valve Mark”
Engineering standards:
GB50243-2002 “Code for Construction Quality Acceptance of Ventilation and Air Conditioning Engineering”
GB50242-2002 “Code for Acceptance of Construction Quality of Building Water Supply and Drainage and Heating Engineering”
10 development direction
Streamlined development
- Simplify the control loop
The previous actuators used a large number of pneumatic and electric control circuits, which increased the complexity of the system, while the pilot solenoid valve formed a control circuit using the working medium itself in the valve, and the structure was very simple. In the past, many technical parameters of solenoid valves at home and abroad were still restricted. The diameter of domestic solenoid valves has been expanded to 30Omm; the temperature of the medium is as low as 200℃ and as high as 450℃; the working pressure is from vacuum to 25MPa. The action time ranges from ten seconds to several milliseconds. The new development of these technologies can completely replace the original bulky and expensive two-position fast shut-off valve and pneumatic on-off valve, electric on-off valve, and part of the continuously adjustable pneumatic and electric control valve. Foreign textile, light industry, urban construction and other industries have switched to solenoid valves in large numbers, while metallurgy and chemical industries have taken the lead in using more and more solenoid valves in auxiliary systems. Domestic automatic control professionals have paid more and more attention to solenoid valves.
- Simplify the piping system
When the automatic control valve is working, some auxiliary valves and pipe fittings must be equipped in the pipeline.
A filter must be installed in front of the automatic control valve. The combined use of multiple automatic control valves often requires the installation of check valves to prevent interference between pipelines. One-way solenoid valves, combined solenoid valves and solenoid valves with filters have all played a role in simplifying pipelines.
- Simplify the structure and process of wide doors
The solenoid valve is an automatic control valve with simple principle and structure, but it needs to be further simplified.
The structure and technology of the solenoid valves for washing machines and refrigerators in the home appliance industry are suitable for mass production. Common solenoid valve coil components have been plastic encapsulated to reduce the failure of lead wire breakage, and it is easy to achieve protection requirements such as waterproof and explosion-proof. The valve body, valve cover and other parts have adopted precision casting, forging and other processes, and engineering plastic solenoid valves have also been put on the market in batches. Domestic explosion-proof solenoid valves are not only flameproof, but also encapsulated and intrinsically safe. High pressure and high temperature solenoid valves have also appeared to simplify the structure and process.
Development in the direction of intelligence
This mainly refers to how the solenoid valve can better cooperate with the intelligent instrument to improve the control accuracy and reliability of the system.
It is generally believed that positional adjustment is difficult to achieve very high accuracy, but in many occasions, using appropriate methods can achieve the required high accuracy, which greatly saves costs.
- Double combination electromagnetic wide.
This is a combination of solenoid valves of different sizes.
The oil metering accuracy of a large number of dispensers is as high as 0.02%, and they all use double solenoid valves. The large valve is opened, making the refueling close to completion in a short time; then the large valve is closed, and the small valve is supplemented to ensure flow accuracy.
By the way, it is pointed out that the large flow metering of domestic oil depots is still introducing or imitating foreign multi-stage shut-off valves with more complicated structures and less stable performance. This kind of product is not made by world-renowned professional companies because the market demand has not reached enough to attract them. interest. In fact, our oil depot adopts domestically produced large-flow double-combination valve, the effect will be much better.
Duplex combination valves are also commonly used to control temperature, pressure, liquid level and other parameters. The large valve guarantees the basic quantity, and the small valve provides the compensation quantity. In a system with relatively stable parameters, this type of position control can achieve quite high accuracy. For many systems with large changes in parameters, the rate of change is still restricted. For example, temperature control systems are still affected by thermal inertia. Therefore, a properly used double combination valve can greatly reduce the cost compared with the regulating valve under the premise of meeting the control requirements.
- Three-position solenoid valve and digital valve
The spool of the three-position solenoid valve has three working positions. It is usually not energized and in a slightly open state, and the valve provides initial flow; for one electrical signal, the solenoid valve is fully opened and provides large flow; for another electrical signal, the valve closes . The valve also has a manual device, which makes it unnecessary to consume electricity when the valve is closed for a long time. The three-position solenoid valve can be regarded as a double solenoid valve with a more compact structure. It can easily achieve three-position adjustment and has been used in many applications.
A further idea is that n solenoid valves of a certain size constitute 2n kinds of flow, similar to the digital circuit, this combination valve is called a digital valve. In fact, two double valves or three-position valves with different sizes can produce 24=16 or 32=9 kinds of flow, which can reach very high accuracy. In principle, it has advantages in supporting industrial computers, but because the application field has not yet put forward a large number of requirements, this technology is still in the experimental stage.
- Self-holding electromagnetic wide
The self-holding solenoid valve completes the opening and closing action of the valve only by energizing in an instant, and the spool position does not need electricity to maintain. Its advantage lies in saving energy, especially in the occasions where batteries are used as power sources, and the temperature rise can be ignored, so that the coil has a long life and has higher safety in high and low temperature, explosion-proof and other occasions. The common ones are mechanical holding and permanent magnet holding, which are divided into double coil and single coil. The single coil magnetic holding structure is the simplest. It is to change the two states of the corresponding valve switch by changing the polarity of the DC power supply. This kind of solenoid valve needs to add a transfer switch to install the coil external wiring separately, and it is very convenient to match with the intelligent instrument. The solenoid valve equipped with IC card precharge gas meter and water meter is one of the keys to the success or failure of the meter. The self-retaining technology is also an important factor for the success or failure of the solenoid valve. The domestic self-retaining solenoid has become increasingly mature.
Development in the direction of generalization
Solenoid valves are widely used, but the conditions of use are very different. The enhancement of general performance reduces the cost of manufacturing, purchase and sale, storage, installation, and maintenance. A big step has been taken in this regard.
- Adjustable response time
The time from when the electric signal is given to the completion of the spool action is called the response time. Different occasions hope that the switching speed is different, and there are four combinations: fast opening and fast closing-used for fast response systems; fast opening and slow closing-used to prevent water hammer; slow opening and fast closing-used for slow start and rapid off; slow Open slowly and close-for smooth transition.
- Extend the medium suitable for solid
Solenoid valves are different from other automatic control valves in that the medium viscosity range is narrow. Therefore, air, water, steam, oil and other media have different structural parameters for pilot solenoid valves; generally speaking, they cannot be universal. However, the ZDF multifunctional solenoid valve uses only a small screw, but achieves the universal use of air, water and oil, and also greatly widens the application range of oil viscosity, which is very popular.
- Adjustable opening and compatible with manual
Solenoid valves are often expected to have manual functions when in use, as a backup in the event of a power failure or failure.
Generally, manual devices can only open the valve manually or close the valve manually, and both are fully manual. The manual device can also preset the valve opening. Generally, the manual can only preset the maximum or minimum opening of the valve, while the full manual can preset the maximum or minimum opening respectively.
Development in the direction of specialization
The sales volume of solenoid valves has surpassed that of control valves, mainly due to the sharp increase in demand for various special solenoid valves. The following are respectively introduced according to the media category:
- Gas solenoid valve
Due to the adjustment of China’s fuel structure, the proportion of gas fuel continues to rise, and the demand for gas solenoid valves is also increasing. There are many types of gas, such as natural gas, industrial gas, city gas, and liquefied petroleum gas, which contain different impurities and corrosion conditions, and have different requirements for valves. Moreover, the pressure levels vary greatly, with compressed natural gas as high as 21-25Mpa, and gas appliance pressure as low as 2Kpa. China has mature products.
It is worth mentioning that dual-fuel vehicles have been continuously promoted in China along with the improvement of environmental protection laws and regulations. Tens of thousands of vehicles have been refitted in 12 cities, and most of them have selected complete sets of imported fuel supply devices, and solenoid valves have also been matched. import. In fact, these solenoid valves are not produced by specialized foreign solenoid valve companies, and the performance test results do not all meet the relevant technical standards of the Chinese gas industry.
- Steam solenoid valve
The steam solenoid valve must first solve the problem of high temperature resistance, and its sealing materials, conductive and magnetic materials must be specially selected. The corrosion of steam pipes is severe and must be taken seriously. More importantly, there is a lot of condensed water in the steam pipeline after get off work in the factory. The solenoid valve needs to be able to operate reliably when gaseous and liquid fluids pass through. The factory inspection has multiple strict procedures.
- Solenoid valve for water
Solenoid valves for water are always considered to be the simplest. In fact, water is divided into tap water, industrial pure water, industrial waste water, irrigation water, sea water and other categories. Its corrosion performance and cleanliness are different, so you should choose different solenoid valves. valve. Although the tap water valve is the most common, the performance requirements of the valve are different for different purposes.
For example, solenoid valves for firefighting are extremely reliable in action, and the consequences should be disastrous if they fail. Even if the ordinary manual valve does not open and close for a long time, it is difficult to open quickly. High-rise buildings have sprung up, and China’s fire solenoid valve technology has also matured.
Another example is that water plants need to use solenoid valves for inverted siphon pipelines. This solenoid valve must work reliably under pressure and vacuum, and there must be no internal leakage, and the water cleanliness is not high. Down, it should still be flexible.
In addition, solenoid valves for sprinkler irrigation are gradually being used with the development of China’s agriculture and gardening industry.
- Solenoid valve for oil
There are many kinds of oil, and seal technology is one of the keys. Oil-resistant rubber is only a category name. Different oils or even the same kind of oil contains different impurities, so you need to choose different oil-resistant rubbers. For example, being able to withstand leaded gasoline is not necessarily resistant to unleaded gasoline. With the increase in sales of special solenoid valves, the service life of special oil-resistant rubber has also been continuously improved.
The viscosity of oil varies greatly, so solenoid valves of different structures must be selected.
High-viscosity oil often circulates at high temperatures, so the solenoid valve has to solve the problem of high temperature resistance. For fuel, explosion-proof requirements must be met.
- Solenoid valve for air conditioner
Air conditioning is divided into heating and cooling. Refrigerants have undergone significant changes. Ammonia and Freon are gradually decreasing, while new types of refrigerants such as lithium bromide are gradually increasing. Related issues such as sealing, corrosion, and life require careful material selection, reasonable design and advanced technology. It is worth mentioning that the air conditioner mainly controls the temperature and humidity by adjusting the air volume, and the continuous adjustment of the valve flow is not completely necessary. Valveless air conditioning systems are also in use, but they are condemned for problems such as condensation and dripping. Therefore, the solenoid valve with simple structure and low price is the most popular choice. Due to the influence of foreign traditions, electric valves with complex structures and difficult torque control are still widely used in China.
11 common types
1, 2-position 2-port universal valve
- Hot water/steam valve
- 2-position 3-port valve
- 2-position 4-port valve
- 2-position 5-port valve
- Intrinsically safe explosion-proof solenoid valve
- Low power solenoid valve
- Manual reset solenoid valve
- Precision micro valve
- Valve position indicator
12 common faults
The solenoid valve is composed of a solenoid coil and a magnetic core, and is a valve body containing one or several holes. When the coil is energized or de-energized, the operation of the magnetic core will cause the fluid to pass through the valve body or be cut off to achieve the purpose of changing the direction of the fluid. The electromagnetic part of the solenoid valve is composed of fixed iron core, moving iron core, coil and other parts; the valve body part is composed of spool valve core, spool valve sleeve, spring base, etc. The solenoid coil is directly installed on the valve body, and the valve body is enclosed in a sealed tube, forming a simple and compact combination. The solenoid valves commonly used in our production include two-position three-way, two-position four-way, two-position five-way, etc. Let me first talk about the meaning of the two positions: for the solenoid valve, it is charged and de-energized, and for the controlled valve, it is open and closed.
The fault of the solenoid vacuum valve will directly affect the action of the switching valve and the regulating valve. The common fault is that the solenoid valve does not operate, which should be investigated from the following aspects:
- The solenoid valve terminal is loose or the thread is off. The solenoid valve must not be energized and the thread can be tightened.
- The solenoid valve coil is burnt out. You can remove the solenoid valve wiring and measure with a multimeter. If it is open, the solenoid valve coil will burn out. The reason is that the coil is damp, causing poor insulation and magnetic leakage, causing excessive current in the coil and burning. Therefore, it is necessary to prevent rainwater from entering the solenoid valve. In addition, if the spring is too hard, the reaction force is too large, the number of turns of the coil is too few, and the suction force is not enough to cause the coil to burn. For emergency treatment, you can turn the manual button on the coil from the “0” position to the “1” position during normal operation to open the valve.
- Solenoid valve jam: the matching gap between the solenoid valve slide valve sleeve and the valve core is very small (less than 0.008mm), generally a single-piece assembly, when mechanical impurities are brought in or there is too little lubricating oil, it is easy to jam . The treatment method can be made by inserting a steel wire through a small hole in the head to make it rebound. The fundamental solution is to remove the solenoid valve, take out the valve core and valve core sleeve, and clean it with CCI4 to make the valve core move flexibly in the valve sleeve. When disassembling, pay attention to the assembly sequence of the components and the position of the external wiring, so that the reassembly and wiring are correct, and check whether the oil spray hole of the lubricator is blocked and whether the lubricating oil is sufficient.
- Air leakage: Air leakage will cause insufficient air pressure, which makes it difficult to open and close the forced valve. The reason is that the sealing gasket is damaged or the slide valve is worn, which causes blow-by in several cavities. When dealing with the fault of the solenoid valve of the switching system, the appropriate time should be selected and the solenoid valve should be dealt with when the solenoid valve is de-energized. If the processing cannot be completed within a switching gap, the switching system can be suspended and handled calmly.