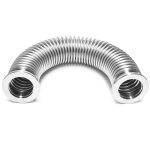
Cryogenic Pump Vacuum System Operation Precautions
(1) In the cryopump system, in order to reduce surface air out, it is necessary to cool the working wall with liquid nitrogen. At this time, however, care should be taken when interpreting the ionization gauge readings. Even if the walls are not cooling, the position of the gauge in the low temperature system is important, especially if it is directly facing the pump. Since the ionization gauge measures gas density instead of pressure, if the temperature of the gas in the gauge is T1 and the temperature in the system is T2, then the pressure reading of the ionization gauge is Pi = P (T1 / T2) 1/2, where P is within the system pressure.
(2) Special attention should be paid when baking the cryopump vacuum system. Because the cryopump is afraid of heat radiation, when the system is baked to 450 ° C, the temperature of the pump may rise above the working range. Water-cooled baffles are inserted as a shield for heat radiation, but this can severely reduce pumping speed. The baffle can be made into a structure similar to a butterfly valve when the baffle is rotated to a shielding position during baking and then rotated back. When the baffle is in the shield position, the pumping speed of the system is reduced by 75%.
(3) When the pumping system is operating, the operator of the system should ensure that the thermal load of the cryopump does not exceed the rated index during the work, and special attention should be paid to the thermal load on the first-stage adsorption plate of the pump. In order to ensure that the thermal load of the cryopump does not exceed the target (especially the thermal load on the first stage), some form of baffle should be used to reduce the amount of radiation hitting the first stage. In addition to the 300 K radiation near the vacuum chamber wall, the first stage also receives heat radiation sources such as coating chambers, heating filaments or sputtering discharges. In many processes the thermal load can be as high as 100 to 150 W, at which point it is easy to exceed the capacity of an expander with a power of 35 to 40 W. It is therefore necessary to add some form of baffle to reduce the radiant flux to the first stage. The easiest way is to use a reflective uncooled baffle. If this is not enough, a herringbone baffle with cooling is required. This baffle can be cooled with water or liquid nitrogen.
(4) In the continuous operation of the cryopump, especially when the adsorbent is saturated with helium, special attention should be paid to prevent instantaneous power failure, because even if there is a short-term power failure, helium will be released from the adsorbent, and the vacuum A large amount of heat on the wall is transferred to the suction surface. At this time, even if the system has been roughly pumped to 20 Pa, it cannot solve the problem, because that is not enough to prevent continuous heat conduction.
If a short-time power failure occurs, that is, after the helium is burst, the pump can no longer continue to work and needs to be regenerated. If the power outage is longer, water vapor may be released from the first stage and deposited on the second stage to saturate the adsorbent, which needs to be completely regenerated.
(5) During operation, the overpressure safety valve of the cryopump should be checked frequently to prevent the safety valve from malfunctioning and causing harm to the operator and the pump.
(6) Do not use a cryopump to remove toxic or explosive dangerous gases that are prone to chemical reactions. Because a variety of vapors can condense on the low-temperature surface, it can accumulate a large amount of deposits. When the pump is heated, some of the deposits condensed on the low-temperature surface may react with each other or with the atmosphere. For example, silane and water vapor react at 77 K, creating a danger of explosion. If explosive gas is condensed in the pump, when the pump suddenly heats up and a large amount of gas is released, they will flow into the evacuated system. At this time, if the ionization gauge is working, serious problems will occur.
(7) The pumping capacity of cryogenic pumps for all gases is not the same. The ability of the cryopump to pump helium and hydrogen is much worse than the ability to pump other gases. This should be considered in the composition and operation of the system.
(8) The compressor needs to be filled with high-purity helium (99.999%). Neon is the most common impurity in helium, it condenses on low-temperature levels and causes seal wear.