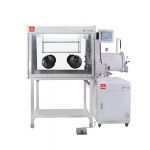
Glove Boxes: The Effects of Gas Permeation and Equilibrium
By Bob Applequist, Senior Application Specialist
On February 01, 2012 in Articles
Controlled Atmosphere Glove Boxes are designed to contain an internal inert gas environment, purified to some level. How to achieve the gas purities requires understanding a few fundamental concerns related to the chemistry and physics of gases.
Most often misunderstood, and/or overlooked, are the properties of gas permeation and equilibrium. Physics describes permeation as the movement or penetration of gas molecules through a solid substance. All solid materials (glass, plastics and steel) are permeable to some degree. This includes the material used in constructing glove boxes.
A simple fact of physics is that a gas at a high concentration within an environment chamber will migrate or permeate through any solid material into another adjacent environment chamber containing a lower concentration of that gas. This is gas permeation which ultimately leads to gas equilibrium.
Gases will always achieve an equilibrium concentration between two separated environments or chambers. Once equilibrium is achieved, gas concentrations reach a steady state. In other words a very contaminant-free gas environment will not stay that way regardless of how “leak tight” the chambers are.
Contaminant gases will permeate through the solid material of any glove box wall until a steady state or equilibrium of gas concentration is reached. It is this particular fact that separates all glove boxes made of various different materials.
The permeation effect requires glove boxes to have a contaminant removal system if very low levels of oxygen and moisture/water must be achieved and constantly maintained in an inert gas environment. The removal system must essentially compensate for the continuous contamination rate in order to keep the glove box clean.
Depending on the purity and time required for a glove box application, contaminant removal systems can be simple accessories—such as a molecular sieve for water adsorption or complicated copper and molecular sieve removing systems. Generally these systems can be recharged in-place, saving significant costs in replacing the removal catalysts after they become saturated.