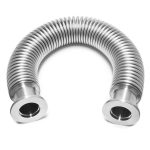
Detailed Analysis of Stainless Steel Bellows Welding Steps
Stainless steel bellows hose requires very high welding technology; if the welding technology is not mature, it may cause perforation, water leakage, rust and other problems in the bellows.
Many people don’t know how to weld vacuum bellows. Today, let us explain it to you.
Bellows welding technology is divided into TIG welding and MIG welding, and the difference between the two is that MIG uses metal wire, while TIG uses tungsten electrodes in the welding torch.
TIG welding: TIG welding has better air-tightness and can reduce pressure vessel welding. Welding is the pore of the weld. The heat source is DC arc, the working voltage is 10-95 volts, and the current can reach 600 amperes. It is mostly used on medium-thickness workpieces.
MIG welding: an arc welding method in which an external gas is used as the arc medium, and the metal droplet is protected, and the high temperature metal in the welding zone is protected.
Stainless steel welding can be divided into five steps:
1: Nozzle size When welding, you must first measure the length of the pipe, and then use a pipe cutter to cut the size of the pipe.
2: Cleaning the pipeline. Because the pipeline is of metal nature, some waste residues should be generated in the pipe due to oxidation, and some waste residues will affect the welding effect. Therefore, before welding, use emery cloth or paper to grind away the waste slag in the pipe.
3: Use the tube brush to clean the accessories. The cleaning accessories can make the welding hose ensure clean and tin-plated joints.
4: Master the welding time Generally speaking, how long the welding pipe you need, you need the corresponding length of solder.
5: Use the torch heat pipe The main purpose of the torch heat pipe is to ensure that the welding part of the pipeline is evenly heated. Make sure that the flame is close enough to cover the entire pipe diameter.