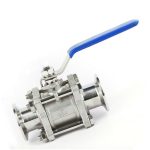
Floating Ball Valve Standards and Structural Features
Structural characteristics of floating ball valve
- Unique valve seat sealing structure. Years of ball valve manufacturing experience combined with advanced technology at home and abroad designed the double-line sealing valve seat to reliably ensure the valve seal. Professional valve seat processing makes the friction coefficient of the valve seat low and the valve operating torque is small.
- The head of the handle valve stem that can indicate the switch state of the valve adopts a flat square structure, and the connection with the handle will not be misaligned, so as to ensure that the direction of the flow hole of the handle and the ball is consistent. When the handle is parallel to the valve pipeline, the valve is in the open state; when the handle is perpendicular to the valve pipeline, the valve is in the closed state.
- Locking device In order to prevent the valve switch from being wrongly actuated and unpredictable line vibration, there are lock holes in the fully open and fully closed positions of the valve, and the valve can be locked with a padlock. Especially when the valve is installed in the field or in the production line of flammable medium petroleum and chemical drugs, the locking device will show its unique advantages.
- The valve stem anti-fly structure. When the pressure in the valve cavity rises, the pressure in the valve body cavity may push the valve stem out. In order to prevent this from happening, a shoulder is provided at the lower part of the valve stem, and the valve stem is installed from the inside of the valve body to prevent the valve stem from flying out. In this way, it is more convenient and safe to replace the packing. At the same time, after a fire, the pressure of the medium will make the valve stem flange and the upper sealing surface of the valve body come into close contact, preventing a large amount of medium from leaking from the damaged packing part and playing an instantaneous sealing effect.
- Anti-static design When operating the valve, due to the friction between the ball and the valve seat, static electricity will be generated and accumulated on the ball. In order to prevent the generation of static sparks, an anti-static device is specially installed on the valve to remove the static electricity generated during the switching process. This design can effectively prevent accidents when the valve is used in gasoline, natural gas, propane, etc. with lower ignition points.
- The middle flange (the connection between the valve body and the left body) has no leakage structure. The connection between the valve body and the left body is sealed by gaskets. In order to prevent leakage due to fire, high temperature or vibration, it is specially designed The valve body is in contact with the metal-metal on the left body to form a fixed orifice flange to ensure no leakage.
- Fire protection structure When a fire accident occurs, non-metallic materials such as valve seats and packing will be burned out, and a large amount of leaked media may further promote the fire. The fireproof structure of the valve can prevent a large amount of medium leakage. After the fire, the leakage parts (ball and valve body, valve stem and valve body, middle flange) are designed to be in contact with metal to meet the fire protection requirements. As shown in the figure, once the valve seat is burned, the ball will directly contact the metal surface of the valve body under pressure, thereby preventing a large amount of medium from leaking from the burned valve seat.
- Pressure-temperature rating
The pressure and temperature rating of the ball valve is not only related to the shell material, but also more closely related to the sealing material such as valve seat, packing and gasket. The seal can be polymer material, asbestos or rubber. The choice of seal material depends on the medium composition, working temperature, working pressure and flow rate of the valve.