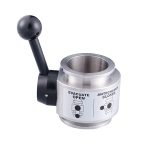
Common Faults and Preventive Measures of Valves
- Stuffing box leakage
This is the main aspect of running, running, dripping, and leaking, which is often seen in factories.
The reasons for stuffing box leakage are as follows:
①The packing is not compatible with the corrosiveness, temperature and pressure of the working medium; ②The filling method is wrong, especially if the whole packing is placed in a circle, it is most likely to cause leakage; ③The valve stem has insufficient machining accuracy or surface finish, or has ovality, There may be nicks; ④The valve stem has been pitted or rusted due to lack of protection in the open air; ⑤The valve stem is bent; ⑥The packing has been used for too long and has aged; ⑦The operation is too fierce.
The method to eliminate packing leakage is: ①Select the packing correctly; ②Filling according to the correct; ③If the valve stem is unqualified, repair or replace, and the surface finish should reach ▽5, and more importantly, it should reach ▽8 or more. And there are no other defects; ④ Take protective measures to prevent corrosion, and replace the ones that have been rusted; ⑤ Straighten or update the valve stem when bent; ⑥ Replace the packing after a certain period of use; ⑦ Pay attention to stable operation, slow opening and closing, Prevent sudden temperature changes or medium impact.
- Leakage of closing parts
Usually the stuffing box leakage is called external leakage, and the closure is called internal leakage. Leakage of the closing part is not easy to find in the valve.
The leakage of the closing parts can be divided into two categories: one is the leakage of the sealing surface, and the other is the leakage of the root of the sealing ring.
The reasons for the leakage are: ①The sealing surface is not well ground; ②The sealing ring is not tightly matched with the valve seat and the valve disc; ③The connection between the valve disc and the valve stem is not strong*; ④The valve stem is bent and twisted, which makes the upper and lower closing parts misalign ⑤Closed too fast, the sealing surface is not in good contact or has long been damaged; ⑥Improper material selection, can not withstand the corrosion of the medium; ⑦Use stop valves and gate valves as regulating valves. The sealing surface cannot withstand the erosion of the high-speed flowing medium; ⑧Some mediums gradually cool down after the valve is closed, causing the sealing surface to appear fine cracks, which will also cause erosion; ⑨Some sealing surfaces and the valve seat, disc The threaded connection is used to easily produce the oxygen concentration difference battery, which will be loosened by corrosion; ⑩The valve core cannot be closed due to the embedding of welding slag, rust, dust and other impurities, or the mechanical parts in the production system fall off and block the valve core.
Prevention methods are:
①Before use, you must carefully test the pressure and leak. If you find that the sealing surface or the root of the sealing ring leaks, you must deal with it before use; ②Check in advance whether the valve parts are intact, and do not use the valve stem to bend or twist or connect the valve stem to the valve stem. Valves that cannot be used; ③The valve should be closed tightly, not violently. If you find that the contact between the sealing surfaces is not good or obstructed, you should open it for a while to let the sundries flow out, and then close it carefully; ④When selecting the valve , Not only the corrosion resistance of the valve body, but also the corrosion resistance of the closing parts should be considered; ⑤ According to the structural characteristics of the valve, the correct use should be used for the parts that need to adjust the flow rate. The regulating valve should be used; ⑥For the cooling of the medium after closing the valve and In the case of a large temperature difference, close the valve tightly after cooling; ⑦When the valve seat, valve disc and sealing ring are connected by threads, PTFE tape can be used as the filler between the threads to make no gaps; ⑧Yes For valves that may fall into impurities, a filter should be added before the valve.
- Valve stem lifting failure
The reasons for valve stem lifting failure are:
①Excessive manipulation causes thread damage; ②Lack of lubrication or lubricant failure; ③Bending and twisting of the valve stem; ④Insufficient surface finish; ⑤Inaccurate fit tolerances, biting too tightly; ⑥Stem nut tilting; ⑦Improper selection of materials, for example The stem and the stem nut are made of the same material, which is easy to bite; ⑧The thread is corroded by the medium (referring to the dark stem valve or the valve with the stem nut in the lower part); ⑨The open-air valve lacks protection, and the stem thread is stained with dust or sand. Corroded by rain, dew, frost and snow.
Methods of prevention:
① Operate carefully, do not use violent force when closing, do not reach the top dead center when opening, turn the handwheel one or two turns after opening enough to make the upper side of the thread tightly, so as to prevent the medium from pushing the valve stem upward impact; ②Check the lubrication frequently, Keep the normal lubrication state; ③Do not use long levers to open and close the valve. Workers who are accustomed to using short levers should strictly control the force to prevent twisting the valve stem (referring to the valve that is directly connected to the hand wheel and the valve stem); ④Improve processing or The repair quality meets the specification requirements; ⑤Materials should be corrosion resistant and adapt to working temperature and other working conditions; ⑥Stem nut should not be made of the same material as the valve stem; ⑦When using plastic as stem nut, check the strength and not only consider Good corrosion resistance and low friction coefficient. Strength must be considered. If the strength is not enough, do not use it; ⑧ Open-air valves should be equipped with a valve stem protective sleeve; ⑨ For normally open valves, turn the handwheel regularly to prevent the stem from rusting.
- Other
Gasket leakage: The main reason is that it is not resistant to corrosion and does not adapt to working temperature and pressure; there are also temperature changes in high-temperature valves. Prevention method: Use gaskets that are suitable for working conditions. For new valves, check whether the gasket material is suitable. If not, replace it. For high-temperature valves, tighten the bolts again during use.
Valve body cracking: generally caused by freezing. When it is cold, the valve must have heat preservation measures, otherwise the water in the valve and the connecting pipeline should be drained after the production is stopped (if there is a plug at the bottom of the valve, the plug can be opened to drain).
Handwheel damage: caused by impact or strong operation of a long lever. It can be avoided as long as the operator and other relevant personnel pay attention.
Packing gland fracture: uneven force when pressing packing, or gland (usually cast iron) is defective. To compress the packing, rotate the screws symmetrically, not skewed. Attention should be paid to not only large and critical parts, but also minor parts such as glands, otherwise it will affect the use.
The connection failure of the valve stem and the valve plate: The gate valve adopts the connection form of the long square head of the valve stem and the T-shaped groove of the gate plate. Sometimes the T-shaped groove is not processed, so the long square head of the valve stem wears faster. Mainly from the manufacturing aspect to solve. But the user can also make up the T-slot to give it a certain smoothness.
The gate of the double gate valve cannot be pressed tightly against the cover: the tension of the double gate is caused by the top wedge. Some gate valves have poor top wedge material (low grade cast iron) and wear or break soon after use. The top wedge is a small piece, not many materials are used, the user can use carbon steel to make it by himself, replacing the original cast iron.