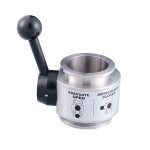
Cause Analysis and Solutions for Common Problems of Steam Pressure Reducing Valve
Chapter 1: Unreasonable product design
Chapter Two: Unreasonable selection of production technology and materials
Chapter Three, the impact of large flow changes on the pressure reducing valve
Chapter 4, the influence of too much pressure difference on the pressure reducing valve
Chapter 5 Precautions for Selection of Various Types of Pressure Reducing Valves
Chapter 1: Unreasonable product design
The theoretical basis adopted in product design is incorrect. Steam is a high-temperature compressible vaporous fluid that is prone to flash vaporization or liquefaction, rather than a fluid in the general sense. When designing a product, it is necessary to consider the negative effects brought about by its many special factors, such as flashing, cavitation, cavitation, water hammer and two-phase flow, etc., otherwise the product quality will be easily unstable. Common problems such as short life span and inability to continue normal use. Designers often apply the general principles of fluid mechanics to the design of steam pressure reducing valves, and ignore the important correction factors required by the particularity of the steam medium, such as critical pressure, compressibility, specific enthalpy and other important parameters. The lack of parameter design will directly lead to a great shortening of the product design life, which cannot meet the basic use of users.
Chapter Two: Unreasonable selection of production technology and materials
Due to cost considerations during product production, some manufacturers failed to consider the particularity of the vapor medium (high temperature, high pressure, and high flow rate). For materials, especially sealing surface materials, which have a very high erosion rate, general materials are used instead Erosion-resistant materials, the process does not consider the extremely detailed requirements of steam for the process, etc., which causes the phenomenon of repeated failures in the field of steam.
Chapter Three, the impact of large flow changes on the pressure reducing valve:
If the steam flow rate changes greatly, it will cause great damage to the pressure reducing valve. Analyze from two situations:
3.1 If the pressure reducing valve is selected according to the maximum flow rate:
1) When the total load of the equipment is very large and a lot of steam is needed, the pressure reducing valve can work normally and the control pressure is accurate;
2) When the total load of the equipment is small or there are other heating devices supplying heat at the same time, the amount of steam required is small, so that the opening of the pressure reducing valve is always in a small opening range, and the clearance of the piston is very small. And the stroke of the piston is too concentrated in a certain area, causing excessive wear in this area very early, resulting in leakage and jamming at the piston and piston sleeve, which will cause problems such as unstable and inaccurate pressure control, and even Serious consequences of the failure of the pressure reducing valve. In addition, on the one hand, because the steam will flash in the valve (at the main valve orifice) when the steam is decompressed, the flash steam will cause cavitation and cavitation on the valve seat sealing surface of the valve, causing the valve and valve The material on the seat surface is impacted into honeycomb-shaped pores, causing vibration and noise (for details, please refer to the technical text of “About Cavitation and Erosion Prone to Parts and Their Effects on Valves”); on the other hand, due to the main valve The opening of the valve is very small (when the valve disc is too close to the valve seat), when wet steam flows at a high speed, it will produce wire and erosion, which will seriously damage the sealing surface. At the same time, any slight movement of the valve core will cause large fluctuations in the flow through the valve. , Making it difficult for the valve to accurately control the pressure.
3.2 If the pressure reducing valve is selected according to the smaller flow rate
1) When the total load of the equipment is small, the pressure reducing valve can work normally and the control pressure is accurate;
2) When the total equipment load is large, the pressure reducing valve is obviously in a state of too small selection, the steam supply is insufficient, and the actual pressure will be lower than the set pressure. Because the main valve has been at its maximum opening for a long time, excessive wear on the top of the piston will result in a jam. Moreover, the main valve spring is also in a state of extreme compression for a long time, which greatly shortens its service life. When selecting the pressure reducing valve, it is generally considered that the operating range of the main valve is controlled between 30-70%.
3.3 Solution—About the parallel pressure reducing station
1) If the normal working flow rate is 300kg/h, the maximum flow rate is 1400 kg/h, the inlet pressure is 8BarG, and the set pressure is 3BarG, the solution is as follows: use a pressure reducing station with two pressure reducing valves in parallel , The total flow of the two pressure reducing valves is 1460 kg/h, one is DN20 with a set pressure of 3BarG, and the other is DN25 with a set pressure of 2.6BarG. When working at a small flow rate, only the DN20 pressure reducing valve is activated. When the demand flow is the largest, the two valves are opened at the same time; when the flow is reduced, the DN25 pressure reducing valve is closed first, and the pressure is controlled separately by the DN20 pressure reducing valve.
2) The parallel pressure reducing station is also used in another working condition, that is, the process conditions are very strict and harsh, and no downtime is allowed. The two sets of pressure reducing valves are one for use and one for backup.
Chapter 4, the influence of too much pressure difference on the pressure reducing valve
The pressure reducing ratio of the pressure reducing valve is mostly 10:1. If the pressure reducing ratio is too large and the pressure difference is greater than 8Bar, it will cause great damage to the pressure reducing valve.
4.1. The pressure reducing valve will have a rated leakage standard under different pressures. Generally, the leakage will not exceed 3%. If the pressure reducing valve needs to be reduced from 16 Barg to 1.6 BarG, this is the limit state use of the pressure reducing valve. It is very likely that the allowable leakage under 16 Barg has reached the flow rate under the pressure of 1.5 Barg. , If there is some leakage, assuming that the pressure has increased to 2 Barg, it is already greater than the 1.6 BarG set at the back end, which will cause the pilot valve to be automatically opened, which cannot guarantee the stable and accurate control of the back end pressure. When this happens, the back-end pressure will cause the pilot valve diaphragm and the adjustment spring to perform frequent automatic corrections. As a result, the pilot valve must be adjusted too frequently, so the pilot valve is particularly prone to wear.
It should be supplemented here that the pilot-operated pressure reducing valve is divided into piston type and diaphragm type. When the pressure difference is large, as mentioned above, the pilot valve of the piston type pressure reducing valve is very easy to wear, and the diaphragm type pressure reducing valve In addition to the pilot valve being very easy to wear, the life of the main valve diaphragm is also greatly shortened, and it is easier to rupture. These components are precisely the most critical parts of the pressure reducing valve. Therefore, the life of the pressure reducing valve is shortened to only It can be used for several months (some users need to replace the parts package within half a year), and the life of the pressure reducing valve used for normal pressure difference is more than 5 years!
4.2 Solution—About the series decompression station
If the normal working flow is 3000kg/h, the inlet pressure is 15BarG, and the set pressure is 3BarG, the following solution is used: the pressure difference of the pressure reducing valve is too large, and two pressure reducing stations connected in series are used. Choose DN40 for the first pressure reducing valve, set the pressure to 8bar, and when reducing from 15 to 8bar, the maximum flow is 3300kg/h; choose DN50 for the second pressure reducing valve, set to 3bar, and set the pressure from 8 When reduced to 3bar, the maximum flow rate is 3030kg/h. The distance between each pressure reducing valve and the rear feedback pipe (copper pipe) needs to be 1.2M. The pressure gauge is installed at the rear end of the pipe. The distance between the two pressure reducing valves is at least 1.5M or more. If the installation position is not enough, two When the distance between the two pressure reducing valves is far, the upstream and downstream of each pressure reducing valve must be installed with a separate shut-off valve.
4.3 If the above two situations occur at the same time, when there is a large flow change and a large pressure difference, a series-parallel combined pressure reducing station is used.
Chapter 5, various types of pressure reducing valve selection and installation considerations
5.1 From the description in 3.1 above, if the pressure reducing valve is too large, the valve will be in a small opening state for a long time, which will cause excessive erosion of the sealing surface, which will affect the service life and sealing effect. If the pressure reducing valve is too small, the steam supply is insufficient and the set pressure cannot be reached. For the pilot-operated pressure reducing valve, the practice of selecting the type according to the pipe diameter should be eliminated.
5.2 For flow parameters, it must be considered separately according to normal flow, maximum flow and minimum flow; for pressure, while considering the pressure reduction ratio, the pressure difference needs to be controlled within the pressure difference range designed and specified by each manufacturer within. When the decompression is relatively large or the flow rate changes greatly in a jump, multiple valves can be used in series or in parallel, or both in series and in parallel. The correctly selected valve is not easy to wear and the pressure control is accurate.
5.3 Although the reliability and accuracy of the pressure reducing valve depend on the correct selection, correct installation is also very important. Unreasonable installation will also bring a lot of troubles. The copper pipe of the pressure reducing valve must be installed at least 1M away from the pressure reducing valve, and the pressure gauge is installed at the rear end of the pipe. The installation and commissioning of some combined decompression stations should be implemented according to the correct design plan.
5.4 A filter must be installed before each pressure reducing valve, and the pipeline must be drained before each pressure reducing station.